I’ll attempt to answer most questions about the basics here, and the technical section will provide more information about what you’d need to know if you wanted me to make some records for you. If you’re already au-fait with lathe cuts, and just want to know what I can and can’t do compared to other outfits, scroll right down to the bottom and there’ll be info there. Some of you may already know some or all of this, and a lot of it has been written about many times before, but this is my personal take on it all. Right, here we go.
Who are you?

I’m Ben. Obsessive record collector for 45+ years, ex-DJ, musician of sorts with a few commercial releases to his name and.. er… other things. I also now make records in addition to the sounds that go on them.
What’s all this ‘lathe cut’ business then?
‘Lathe cut’ records are becoming more commonplace today for various reasons, as demand on the few remaining traditional record pressing plants increases, prices rise and resources dwindle, plus the market opens up for really limited runs of records. Even with the whole ‘vinyl is back, back, BACK’ hype of the past decade or so, many small labels and individuals find that it’s still jolly difficult to sell physical objects to people these days. Getting a pressing plant to run off less than 200-300 copies of something isn’t easy (2023 edit: see footnote). Lathe cut records aren’t necessarily a ‘cheap’ alternative option, but you’re less likely to end up with half a pressing run sitting in boxes under the bed for 10 years.
But, ‘lathe cut‘…? Well, I didn’t come up with the term, right?
First off, pretty much all vinyl records start off by being ‘cut’ on a ‘lathe’, with the creation of a master disc which then becomes the basis for hundreds or thousands of copies after some fairly intensive industrial processes. However, ‘lathe cut’ now seems to have become the generally accepted term for making records one at a time, cutting the groove directly into each plastic disc. Each one is therefore unique. This opens up a few interesting possibilities, but let’s not get ahead of ourselves yet.
- 2023 footnote: Well, that was the case when I wrote the original text. At the moment, there are two or three plants offering runs of 100, or even less in one case. Yeah, squash the little guys, why don’t you? So you’ll have to do the sums yourself to see how things stack up with regards to costing if you’re thinking of 50+ records, as there’s a point where it snaps over in their favour (and on LPs that’s pretty low). What I would say in my favour is that I can still do those super low numbers and one offs which they can’t, and you’re absolutely not going to get a whole load of records which are so surface noise-y and off centre as to be unlistenable and possibly unsaleable as they’re being banged out so quickly with no quality checks. Some label-running friends of mine have already discovered this to their cost. Anyway, calming down and moving on…

What’s the difference between ‘lathe cut records’ and acetates, or dubplates?
Terminology and raw materials, really. A traditional acetate is an aluminium disc, coated with cellulose lacquer. In fact, they’re pretty much identical to the master discs which are the first stage in the record pressing process, but they were of a slightly lower grade of finish, and used to create one-offs in various stages of the recording process in major studios. They were once the only way of creating a one-off record, acetate cutting services for private individuals were commonplace from the 1950s to the 1990s, and some people still create them today when they can get hold of blanks (supply has dwindled and they’re very expensive now). A dubplate? Same thing, different name, more kudos in certain scenes. The problem is that the cellulose surface was/is quite soft, and the results could only be played a fairly limited number of times before they literally wore thin. They can sound absolutely amazing, though.

I make records in exactly the same fashion, but rather than into a soft acetate, the grooves are cut into a solid plastic that is more akin to the PVC used for pressed records. The upshot is that they look and feel almost identical to a pressing and, if looked after properly, will last just as long.
Now then… I say ‘more akin’ to PVC, and that’s because the discs I cut aren’t made from your actual polyvinyl chloride. In fact, none of the people offering ‘bespoke vinyl‘ are cutting into polyvinyl chloride. PVC is way too hard to cut a groove into, even with an expensive diamond cutting stylus (which would probably break if you tried it). People cut/emboss grooves into a variety of plastic materials, very often polycarbonate when using the older mono lathes from the ’60s and earlier, however the discs in use here are actually made from PET-G. Polyethylene terephthalate glycol, apparently. This is a bit softer than PVC, which allows it to be cut nicely when heated up a bit, but – if looked after properly – will last for hundreds of plays unlike the traditional dubplate. However, see my note under the ‘scratching’ bit lower down. I could move it up here but I think it makes more sense down there.
Splitting hairs? Perhaps. I feel it necessary to point all this out because:
a) I note a lot of other ‘lathe-cutters’ are advertising that their products are *vinyl*, which would perhaps lead people to believe they’re going to receive a PVC disc. Not the end of the world, perhaps. However, some say flat outright that they’re cutting into PVC (not helped by some blank suppliers talking crap about what their discs are made from, admittedly). They aren’t. But…
b) I also see people saying that PET-G lathe cuts aren’t ‘real records’. Yes they bloody well are. I bet a sizeable majority of the people who say that PET-G lathe cuts aren’t ‘real records’ have loads of rare ’60s and ’70s ‘styrene’ 7″s which were injection moulded rather than pressed, and wear out rather quickly. Are they not ‘real records’ either, then? Pfft… Actually, you know these new ‘EcoRecords’, or this ‘BioVinyl’ stuff? It’s PET plastic, injection moulded instead of pressed in the traditional way. It’s had considerable investment from parts of the major music industry, and they’re not given to chucking their money around on stuff that’s not going to work these days. Or so you’d think. See my notes below about coloured discs below.
Anyway, that brings us on to the matter of…
What do they sound like?
I need to update this bit really, as what I’m cutting now sounds better than what I was cutting 2 years ago when I first started this site up. I’ve left links to the older soundfiles below as they still sounds pretty good, but I’ll replace them eventually when I get the chance. The following videos demonstrate the sound quality I achieve now, and the original text continues afterwards. Apologies if there are adverts on these, and for the huge thumbnail text which seems to be de rigueur these days. I’m trying to adapt to this modern world. Honestly.
Right, here’s the rub. They can sound extremely good. There are some things to bear in mind, though.
Now, I’m not cutting my discs on a lovely old 1970s Neumann or Scully lathe because 1) hardly any of those exist these days, 2) they cost an absolute fortune on the rare occasions they come up for sale, and 3) even if I could find/afford one I wouldn’t have anywhere to put it. It’s a world inhabited by a very lucky few.
The more clued-up people out there may have noticed in the photos that I’m using a T560 VinylRecorder system. It’s a well proven piece of equipment, with many users across the globe. It might appear very basic, but it’s capable of creating remarkably high fidelity records. No, I wouldn’t dare to compare the results with those that can be achieved by an expert cutting engineer using high end equipment, but below here you should find a link to an audio file (wav format)….
In this file are three versions of a piece of my own music: the original mastered digital file, a version I cut myself, and a commercial pressing of it on black vinyl from 2018 – cut and manufactured by a very well known company – in that order. Both the pressed copy and the lathe cut are recorded using the same turntable and cartridge (a 50 year old Shure M75ED, should anyone care). I’ll let you make up your own minds about the differences between them, although bear in mind than comparing a digital file to *any* vinyl record is a bit of an apples/oranges scenario. What was a real surprise to me is that the commercial pressing actually played ever-so-slightly slow…
Here’s another example, 320k mp3 this time. A section of The Great Gig In The Sky from Pink Floyd’s Dark Side Of The Moon, cut onto a 7″ at 45rpm. The source was the original 1987 CD version. I think it sounds quite nice.
One more? How about something that’s very stereo indeed? Here’s a snatch of Stereolab’s University Microfilms, again cut at 45 on a 7″. This is to show that, whilst maybe not having the same amount of width that a professional cutting set-up costing tens of thousands of [insert currency here] might be able to achieve, and certainly not compared to digital files (obviously), my records are definitely not in mono. Unless you wanted them to be, of course.
Obviously, the quality of the end product depends on many things, not least the original material supplied. With digital, you pretty much get out what you put in. With a basic process dating back over a century, and even the technologically refined form going back to the 1950s with little change since, it’s not like that. You can read more about that on the technical page. However, if you supply me with audio that doesn’t have ridiculous amounts of low or high end, isn’t dynamically compressed and brickwalled into a ‘loud’ sonic sausage, and you don’t want me to try and squash 9 minutes of cymbal crashes onto a 7″ single rotating at 33rpm, the results should be quite satisfying.
Funnily enough, I’ve been looking at the websites of other people who do this, and it’s all rather inconsistent. Some say they sound better than pressed records, some say they don’t. They then go on to list all sorts of weird reasons to back up their view. “There may be pops and crackles due to cutting debris…” Well, you’re not making the things right then, are you? “Lathe cut records sound better than pressed records because there are fewer stages in the manufacturing process…” Erm, that’s a rather broad sweep, no?
My view: You get great lathe cuts, you get shit ones. You get great pressings (occasionally), you get shit ones (all too often). I buy a lot of records, and 3 out of 5 times I’m hacked off with the product I receive. Warped discs, off centre stampings, scratches due to careless packing, and even actual sonic and physical faults in the original lacquer cut that somehow nobody managed to notice at the test pressing stage. Put it this way, if I was churning out stuff like that myself, I’d expect to go out of business within weeks. As it is, if a record I make isn’t up to the standard I would expect if I were buying it, it goes in the bin rather than in the post. The standard cutting head on the T560 is quite limited in various ways when compared to the pinnacle of ’70s/’80s disc cutting technology, especially when using the standard hardware which comes with the system. However I threw that stuff out ages ago, and I think I can get far better results out of it than the majority of other people who own them. He said, modestly…

Right. Actually, looking around the internet, there seem to be a lot of people doing what you’re doing.
Yes, it does look like the market in lathe cut record cutting seems to have exploded recently, doesn’t it? Everyone and their cat seems to be at it. Call it bad timing on my part. (2025 edit: Good grief… talk about a groaning bandwagon.)
So, why would I use you?
A tricky one to answer, isn’t it? All I can say is that I’m confident that the discs I make look and sound pretty damned good, within the limitations of this level of equipment, and I’m speaking as a very picky record buyer myself. I may be underseling myself here, but that’s my nature. Have a listen to the sound samples above, compare them to other people’s (if you can find any, that is) and make up your own mind.
Basically, I don’t make crap. Why would I? And I’m constantly trying to make things better still, rather than just bang stuff out. If a record doesn’t sound good, it has no reason or right to exist.
Why aren’t you offering 12″ discs? They’re not in your price list.
The price list needs a major overhaul anyway, but 12″ discs are a nightmare. Because they take so long to do, a full album (up to 40 mins) is going to cost you *around* £30 for a one off, or down to maybe around £20 per copy on a run of the things. Let’s nail that here. No, not cheap. As I said above, on anything over 25 or so you really might be better off looking at a low pressing run, you’ll get 100 discs for not a lot more than I could make 50, and you’d have proper sleeves as well (see below). On a 12″ single, things might well be different. Prices will be dependant on running time, more than anything else. They’re very tricky things to price up, but don’t be afraid to ask, I can usually sort something out.
Can you make 78s?
Er, sort of. If you mean, can I make a record that can play back at 78rpm, then absolutely yes. If you mean, can I make a record that I can play on an old wind-up gramophone with a steel needle, the answer is absolutey no. The plastic discs I use are way too soft, and that needle would just tear them to bits in an instant. I believe some people have been able to make gramophone compatible discs using acrylic, but acrylic is way too hard for my cutting stylus and would wreck it in a very short time.
Incidentally, I don’t actually cut stuff at 78rpm, despite my trusty SP10 being able to rotate at that speed. Rather, the audio will need to be slowed down and re-EQ’d, then cut at 45rpm, so when played back at 78rpm it sounds as it should. Why? Well, frankly cutting at 78rpm is a nightmare. Everything happens *so* much quicker than at 45. There’s more chance of trashing the cutting stylus with the inevitable inconsistencies in the blank disc at the outer edge, the swarf is more likely not to be picked up by the vacuum and end up spilling everywhere, making that lock groove properly is way trickier, etc. etc. My nerves really just can’t stand that sort of abuse anymore. But the advantage is that the resulting disc sounds amazing at 78rpm… kinda like half-speed mastering for singles!
Can I scratch using them or will they fall apart?
You can certainly use them for ‘turntablism’ work, yes. I would warn that the plastic compound the blanks are made from is possibly a little softer than the best pressings (although I have no proof either way on this, I’m not a scientist) so they might develop cue burn a bit faster if heavily used/abused. Now, I can’t say I’ve done any extensive tests in this field, as my ‘skills’ are decidedly lacking in that department, but from the little I’ve tried these discs seem to hold up very well indeed, and tons better than a styrene 45 or acetate!
Note: one thing I would say, and that nobody else seems to, is that the discs are less resistant to general abuse than a PVC record, in that careless handling is more likely to result in an audible blemish. The upshot is, you can play them as much as you like but try not to drag your fingernails across them or chuck them around the room. Unless you want a distressed sound, of course…
I read on another site that you can’t play lathe cuts with an automatic turntable?
That just means they aren’t making their discs properly, i.e. not starting the lead-in groove close enough to the outer edge of the disc. It’s tricky, as the blank discs tend not to be exactly round despite being laser-cut – nothing I have any control over, by the way – so I need to be really careful when setting the cutting stylus down that I’m not going to overshoot the edge and destroy it. Also there can be significant distortion of the outer edge from where the discs have been laser cut, which isn’t good for the stylus. Most people seem to ‘get around’ this by starting the lead-in about 5mm or more from the edge, so it’ll be *your* stylus that’s at risk on an auto player. Here’s one of mine for comparison. The secret? Being ruddy careful, and binning off any discs which are excessively rippled. Not hard.
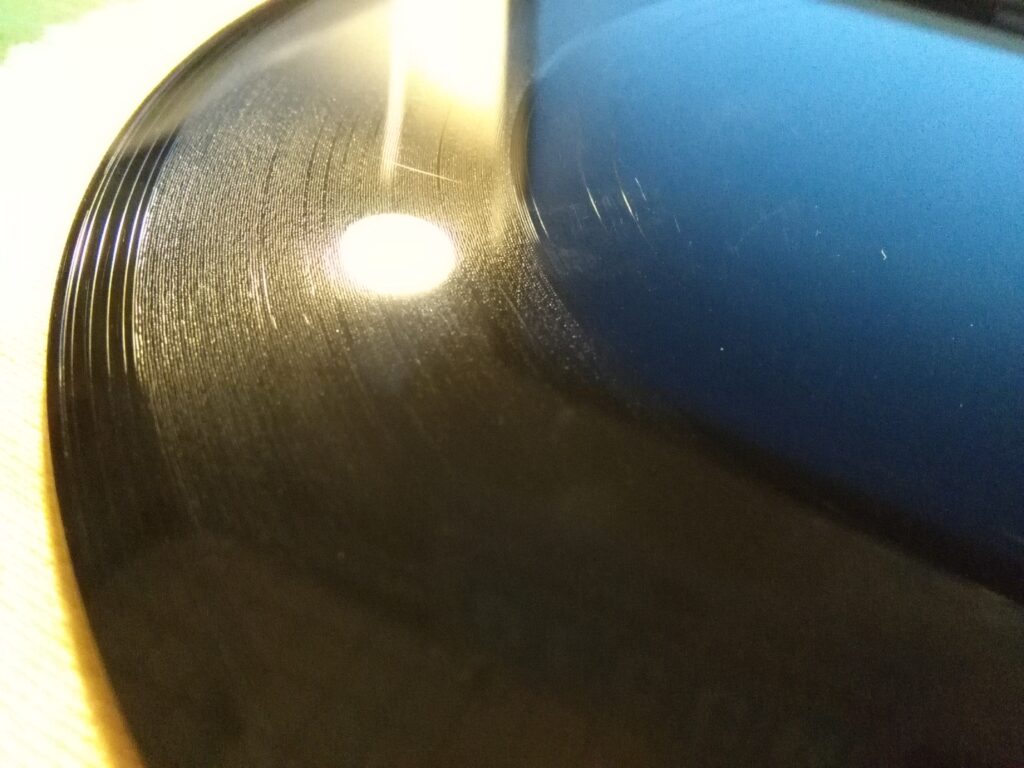
I also read that lathe cuts aren’t as loud as pressed records.
Oh yeah? If they’re embossing rather than cutting, that’s understandable. If they’re cutting rather than embossing, then that’s someone making excuses for their lack of skill. Probably.
I can cut records as ‘loud’ as most conventional pressings, but there’s a limit to how much power I can put through the cutter head on my little setup before something goes pop or starts to distort, especially if there’s a lot of top end on the source material. I can’t risk trying to cut a disc at the super high levels like you might find on an ’80s 12″, but I can easily get a similar overall level to most albums or 7″ singles, unless the material is really problematic sonically, or you’re pushing the running time limits to the maximum. However, there’s more about this in the technical section, and why ‘loud’ isn’t always good. I aim for at least +6db peak as a minimum, under normal circumstances.
Can you make odd sizes and colours?
To an extent, I suppose. I don’t do picture discs, lurid colours or sparkly finish records like some other people. I’m more interested in making damned good sounding records that people can actually play and repeatedly enjoy, rather than crappy sounding novelty items. As things stand I can make discs in black, transparent, solid white and a very lovely translucent red. Black discs come in both 1.5mm and 2mm thickness, the other colours are 2mm only.
It’s also now possible to get custom shapes and sizes from my dear friends at the Spinner Town blank company. Some are off the shelf (like the ones below, that’s not my hand by the way) but any design is theoretically possible, at a cost of course. Ask me, and I’ll ask them, and we’ll see. Remember that you may well be limited as to how much recording time a weird shape can hold, though.
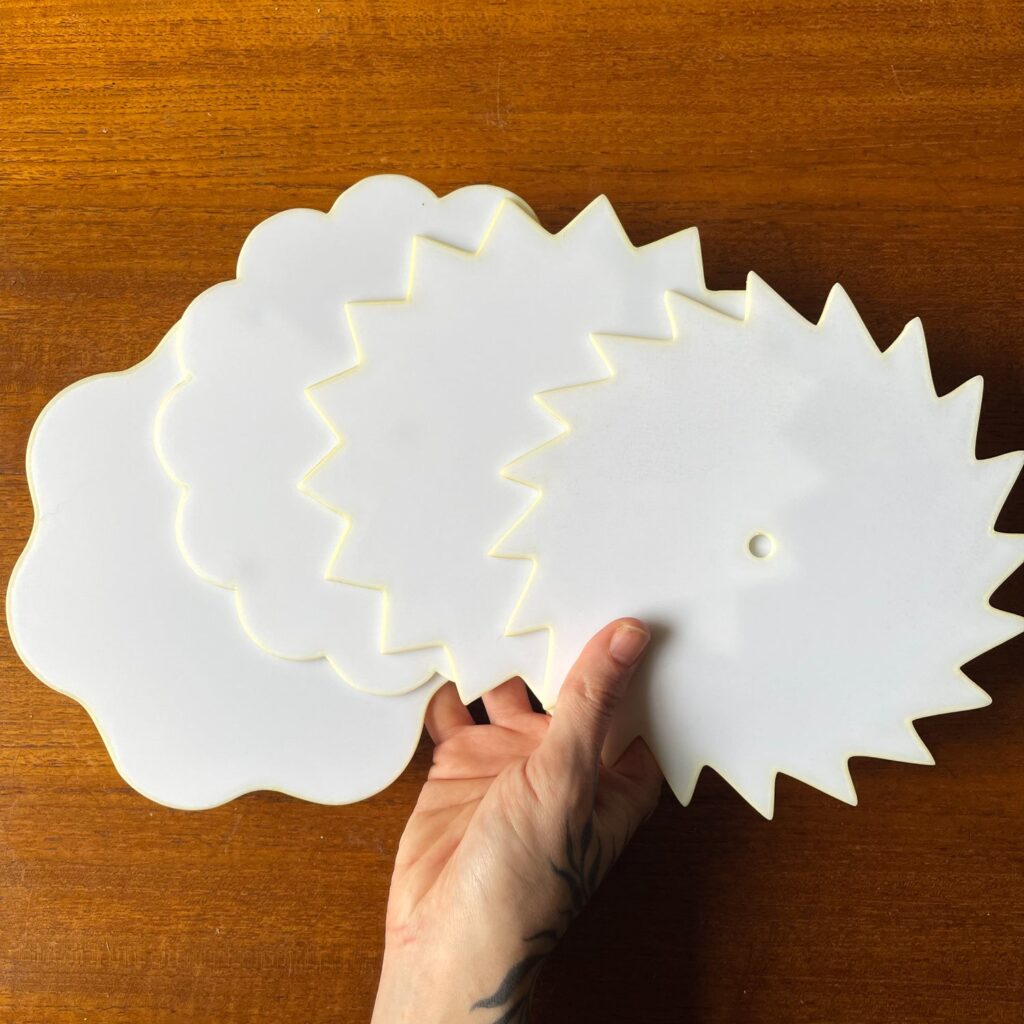
But I’ve just been on [redacted]’s website, and they’re offering all sort of colours now. They look amazing. I’m told that these are going to replace the old style discs and…[snip!]
Yeah, let’s stop right there. Those discs are injection moulded rather than cut from sheet, basically being groove-less versions of the ‘eco-records’ that people like Sonopress and Green Vinyl have been making a big song and dance about. The material is similar (i.e. it’s PET rather than PVC) but the injection process is deeply flawed, grooves or no grooves. Long story short: they’re usually warped to hell, they need a lot of faffing around (and possibly extra equipment) to cut with any sort of success, they eat cutting styli like there’s no tomorrow, and you’d still be getting a finished disc like a bloody rollercoaster at the end of it all… So, forget it. No. If wacky colours are *really* more important than a record which actually sounds any good, then you’ll have to take your business/chances elsewhere.
You said early on they aren’t necessarily a ‘cheap’ option. I just looked at the prices… you weren’t kidding, were you?
No, they aren’t ‘cheap’ in the way that you occasionally used to be able to buy a 7″ single in HMV for 99p, 20+ years ago. But that was 20+ years ago. These days you’d be lucky to be able to buy a 7″ single in HMV for £9.99. However that’s not really the point here anyway, remembering that I make each one of these individually. It’s not just a case of slapping a blank disc on, pressing a couple of buttons and waiting, then throwing it into a card mailer and *ker-ching!*
First off there’s the cost of the blank disc itself, then there’s the time spent working on the audio file to get the best results out of it, then the time spent getting everything prepped, making a test cut (maybe more than one), then the time actually making the final product. That initial prep time is the same no matter if you want one disc or 100. If you’re wanting more than one of the same thing, then obviously we can start to divide that time down per disc, hence the price getting cheaper the more I make.
But then there’s still the time I spend making each subsequent record, the wear/tear on the cutting stylus and other equipment needs to be taken into account (they don’t last forever), electricity costs, the odd Pot Noodle and energy drink to stop me lapsing into unconsciousness etc. We all need to make a living, eh? How much does the average plumber charge per hour?
However, nothing’s set in stone. I know what it’s like in the real world. I’ve not put my prices up in the last five years – despite raw materials increasing in cost and my running costs basically tripling thanks to energy price rises – but that can’t last forever. Talk to me and let’s see what we can do. I’ll not take the p*ss out of anyone, including myself.
How quickly can you make records for me?
The video above shows me making a 7″ single for the excellent Castles In Space label, many years ago when I had time to make videos (note the old SL1200 in use, that’s long been replaced). Each copy, of which there were 100, took the best part of 15 minutes to create.
So, it depends on how many you want, and how long each one is. It’s a real time process. For example: a two-sided 7″ single, with four minutes of audio per side. Obviously it’ll take eight minutes to cut the actual audio, but there’s more to it than that… preparing the blank disc, getting it up to the right temperature for cutting, engaging the lathe, checking everything, creating the runout and resetting the lathe at the end of the side, then repeating the process for the other side. Realistically, it’ll take the best part of an hour to make four of those. That’s after the time needed to assess the material, setup the equipment for it, and generally let everything ‘warm up’. There are no shortcuts. I can give more accurate estimates (??!) if you get in touch with your needs.
Note that I don’t have an automated system where you upload an audio file and your debit card details, and you just sit back and wait for the results to show up in the post. I work person to person, as every record is different and needs a different approach to manufacture. (The word ‘artisan’ really grinds my teeth, and I detest all that ‘hand crafted’ type cobblers that you see hanging on coffee shop walls in a myriad of offensive typefaces, but that is actually what I’m offering here. Yes, Mr. A. Hypocrite, at your service.)
So if you’re interested having some records made, please get in touch via email and we’ll converse. I’m quite an amiable sort of chap, honestly.

Can you do labels and sleeves for me?
Labels… well yes, if you really need me to. I can supply blank labels with discs, either stuck to the records or separate on A4 sheets so you can print/rubber stamp/action paint them yourself. If you’re really stuck for printing options, and have artwork you want to use, then we can maybe sort something out (at extra cost, obviously) but they might not be as nice as a professional printing outfit could manage, or perhaps even yourself. I’ve only got a bog standard desktop inkjet printer, so adjust expectations accordingly. I’ve now got a better system of label printing, using matte sticker paper and one of those desktop cutters, so they look rather better now (colours are more vivid, blacks darker) than when I was using off the shelf label sheets. The paper is now slightly thicker and you may notice the cut line looking at it edge-on, but I think it’s a better option. But if you want to source your own labels, rock on!
As for sleeves, the records come in plain inners as standard. Again, I can source standard plain card sleeves and the like (at cost) but perhaps you’d be better off doing it yourself and getting creative with packaging. Screen printed sheets in poly bags, spray painted card, that sort of thing. It does make it all more special and desirable, at the end of the day. The days of identical injection-moulded records in identical paper sleeves are gone. You’re making your art in the music, why not extend the canvas to the physical object? But sorry to say I simply don’t have the time or resources at the moment to create outer sleeves. Maybe when I’ve got a lovely large workspace and I’ve figured out how to make another two of me.
(For 12″ discs at the moment – early 2025 – I can supply plain black or white sleeves with spines and no centre die-cut holes for a very reasonable price. Ask me, ask me, ask me…)
Can I have a physical test cut?
I get asked this quite a lot. I can understand people wanting to actually see, hold and play an example of my wares, especially before committing to a full run of 30,40,50, whatever. I’ll always (or nearly always) do a test cut (or cuts) anyway, but these tend to get done on otherwise scrap discs – usually one where something went wrong during a cut on one side, or one that’s too warped/raggy to send out as finished product – and are purely a means of checking the sound and for adjustment of any EQ changes, de-essing etc. that I might need to bring into play. Once I’ve got things as good as I can, I’ll do another full cut onto another scrap blank then record that as a digital file – SL1210, properly aligned AT cartridge, NAD phono stage, 16bit 44.1khz – and send it over for checking. So by this point I’ve already probably invested a fair bit of time in the project, and if you then wanted an actual physical record to check you’d basically have to buy one at full whack for a one-off plus postage. Of course, if you were happy with what you got (and why wouldn’t you be?) then I could assimilate that cost back into the run, minus the postage. Anyway, talk to me and we can work it out. We can work it out. Life is very short… [SNIP! – Northern Songs Ltd.]
How do I get my sounds to you?
The easiest way is to upload them in digital format to a service like WeTransfer, send me the link and off we go. Get in touch beforehand though, don’t just throw files at me. WAVs or FLACs are preferable, please don’t send me scrappy 128k mp3s (or worse) as that’ll just prove unsatisfactory to everyone concerned. If you’ve got stuff on analogue tape, I can work from that to some extent (depending on the format – cassette obviously, 1/4″ half track at 7.5 or 15ips, or 1/4″ quarter track at 3.25 or 7ips) but it won’t be going through a warm dusty all-valve signal chain, I’m afraid to say. If you’ve got weirder ideas, well… I’m intrigued!
Any other questions? Get in touch…
TL;DR: basic facts!
- I individually cut hi-fi stereo records onto PET-G blanks
- I can cut 5″, 7″, 8″, 10″ and 12″ diameters (or any other size from 4″ to 14″ by special arrangement)
- I can cut into 1.5mm thick black, and 2mm thick white, transparent and translucent red discs
- I don’t use injection moulded ‘pressed style’ blank discs, no matter what colour they may be
- Shaped discs and engraved designs are options at extra cost, ask for details
- I cannot supply other colours or picture discs at the moment, sorry
- I supply the discs in basic white inner sleeves, various style/size card sleeves are (usually) available at cost
- I can print labels if realy needed, standard inkjet using matt sticker paper
- I cannot make printed outer sleeves of any description at the moment, sorry
- I don’t do ‘mastering’, just as close to a flat transfer from the source material as the equipment will allow